AOG Logistics: Time Critical Strategies for Operational Efficiency
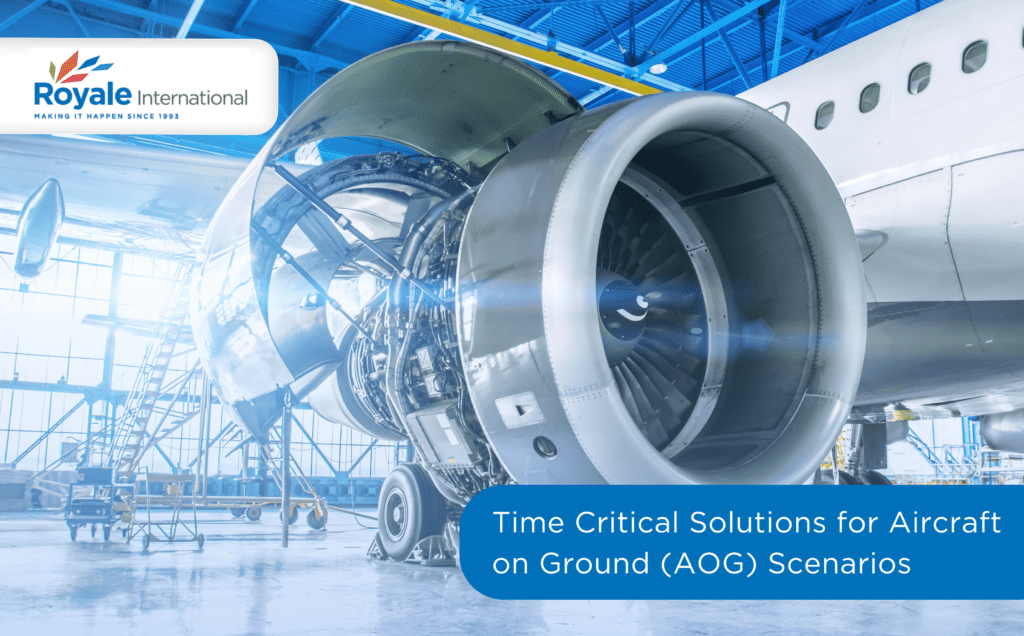
In the fast-paced world of aviation every minute counts. When an aircraft on ground (AOG) situation occurs and there is no trusted AOG logistics provider, the impact on global supply chains is profound. Businesses lose millions due to delayed flights, affecting production materials and end-consumer services.
In this article, we delve into the critical components of Time Critical logistics, including streamlined communication, AOG logistics, and a network of dedicated professionals.
________________________________________________________________________
On the Tarmac Clock: AOGs disrupting global supply chains
When an aircraft is grounded due to mechanical failure, damage, or unforeseen circumstances, AOG logistics becomes crucial for swift resolution and minimising costly downtime.
An aircraft that becomes non-operational due to sudden mechanical failures resulting in the disruption of regular cargo and manufacturing-related shipments. Limited aircraft availability for freight transportation can reduce cargo capacity and increase competition for resources, leading to delayed deliveries and potential financial losses for businesses.
Two key reasons why aircrafts need to be grounded are listed below:
Mechanical issues and component failures
In a time when technology has significantly aided aircraft maintenance, there remain occurrences of mechanical issues and component failures. These failures often demand prompt responses, especially during critical phases like aircraft take-offs and landings.
These issues may arise due to wear and tear, manufacturing defects, or environmental factors. For example, issues with the aircraft’s engines, landing gear, hydraulic systems, or flight control surfaces can all lead to operational disruptions and require immediate attention.
Component failures, on the other hand, refer to the malfunction or breakdown of specific parts or components within the aircraft’s systems. These failures can occur suddenly and unexpectedly, compromising the aircraft’s functionality and safety. Common examples include failures in electrical systems, avionics components, sensors, actuators, and other critical parts that are essential for the aircraft’s operation.
A comprehensive dataset spanning 12 years, which includes 251 accidents and 808 reported incidents involving business jets, sheds light on the gravity of mechanical failures. Of these, 32.7% (82 accidents) and 51.2% (414 incidents) were attributed to mechanical failures.
Despite the diligence of flight crews in following abnormal procedures, incidents underscore the importance of preventive maintenance and thorough pre-flight inspections to mitigate such failures.
Regulatory compliance concerns
Adhering to enforced regulations established by aviation authorities such as the FAA and EASA. These concerns may arise when aircrafts are grounded due to maintenance issues that violate established regulations. Compliance involves addressing airworthiness directives, service bulletins, operational requirements, and maintaining accurate maintenance records. Non-compliance can result in regulatory sanctions or suspension of operating certificates. Time Critical logistics plays a vital role in addressing compliance issues by facilitating the rapid delivery of necessary parts, materials, or documentation to minimize aircraft downtime and ensure timely compliance.
In such cases, every moment counts as businesses face the risk of losing revenue and increasing operational costs. Moreover, delayed shipments can result in dissatisfied customers and damage to brand reputation.
Time Critical logistics is essential for aircraft on ground (AOG) scenarios, as every minute of downtime translates to significant financial losses for airlines and potentially affects passenger schedules.
In such scenarios, Time Critical solutions ensures the swift delivery of urgent spare parts for the grounded aircraft. These spare parts are often vital for the aircraft’s repair and enable it to resume operations promptly.
Time-Critical Logistics: Keeping Aircraft on Ground Scenarios on Schedule
Our Next Flight Out (NFO) services play a pivotal role in reducing downtime for manufacturing businesses, especially those operating in just-in-time environments. Our experts’ longstanding partnerships with various international airlines offer expedited shipping services anywhere around the globe.
By promptly delivering replacement components, NFO minimises aircraft downtime, ensuring operational continuity and on-schedule flights. Navigating AOG scenarios involves selecting the most efficient shipping and urgent delivery methods, adhering to customs and import/export regulations, and meticulously tracking and monitoring shipments to provide real-time updates.
As a global leader in Time Critical logistics solutions, Royale International specialises in meeting the unique demands of the aerospace and aviation sectors, renowned for their emphasis on precision and speed. During critical Aircraft on Ground (AOG) situations, where every moment counts, Time Critical logistics becomes imperative to swiftly deliver much-needed spare parts to grounded aircraft, minimising costly downtime.
Need support for your spare part shipments? handcarry@royaleinternational.com or nfo@royaleinternational.com
Learn how we support the Aerospace Industry through this Case Study.
________________________________________________________________________
For immediate quotations: handcarry@royaleinternational.com or nfo@royaleinternational.com.