Bridging Aviation Logistics Gaps: Royale’s Time Critical Solutions
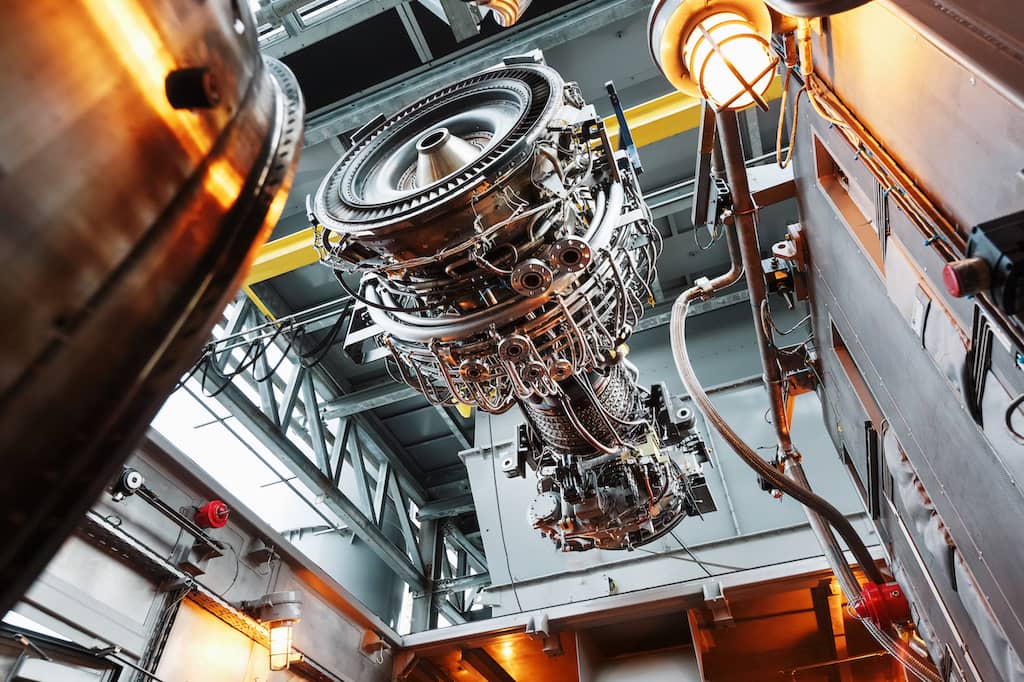
The transport of aircraft engine parts requires attention to detail at every step. The intricacies in aviation manufacturing [or MRO] present in the aviation industry requires an almost flawless approach to logistics. Steps often include careful planning, custom packaging, and coordination of aviation logistics. Planning identifies the most direct and safest route for the aircraft engine part’s journey. Custom packaging is paramount as these aerospace parts are high-value yet delicate items that need protection against potential damage during transit. Once the planning and packaging are taken care of, manufacturers begin to coordinate their logistics. This involves aligning with multiple parties like customs, carriers, and consignees, guarantee that the delivery process is seamless from start to finish. In the post-pandemic era, the increasing number of ageing planes accentuates the vast and varied challenges of logistics.
Dealing with Ageing Aircrafts: A Rising Need for Aircraft Maintenance
As per the statistics published by Statista Research Department, the average age of the active North American aircraft fleet is roughly 10 years with many planes still in service even after 25 years. The projection is that the average age will reach 14 years by 2030. As the aircraft ages, it demands more frequent and meticulous inspections and maintenance, encompassing everything from structural integrity checks to engine part replacements. These maintenance procedures are not only time-consuming but also financially taxing, impacting the bottom line of airlines globally. An aircraft on the ground due to a lack of parts can cost an airline up to $150,000 per hour in lost revenue. So the need for a robust and efficient logistics framework to transport these engine parts quickly and safely. This framework is a crucial aspect of aerospace maintenance.
When dealing with ageing aircraft engines, we encounter three scenarios that urgently require parts.:
- Aircraft-on-Ground (AOG) situations: These are situations where an aircraft is grounded due to technical issues or the need for immediate, critical maintenance. In such cases, to prevent expensive downtime, we must deliver the required parts as quickly as possible. The speed and safety of air freight are unparalleled. This is precisely where our Next Flight Out solutions excel, delivering necessary parts as soon as possible, thereby minimizing downtime.
- Routine maintenance: Scheduled maintenance procedures are regular occurrences in the aviation industry, especially for ageing aircraft. In these instances, parts are usually ordered in advance. However, any delays or mishaps in delivery can disrupt the maintenance schedule, resulting in costly setbacks. In these circumstances, our dedicated account managers come into play. They offer high visibility of shipment tracking and clear communication, minimizing any potential disruptions in your maintenance schedule.
- Unexpected repairs: Despite regular maintenance, older planes can often experience unexpected mechanical issues that require immediate attention. Here, the ability to swiftly procure and transport the needed parts is key to minimizing downtime and ensuring the safety and efficiency of the aircraft. We recognize the importance of every minute and, with our established 24/7/365 Global Control Towers, we can provide you with flight routings in as little as 30 minutes.
Each of these scenarios demands a unique approach in terms of logistics and part delivery, underscoring the need for versatile, efficient, and timely aviation logistics solutions. Transporting aircraft engine parts is a daunting challenge in itself, with several crucial steps needing meticulous attention to detail.
The Detailed Journey of an Aircraft Part: Royale International’s Expertise at Every Stage
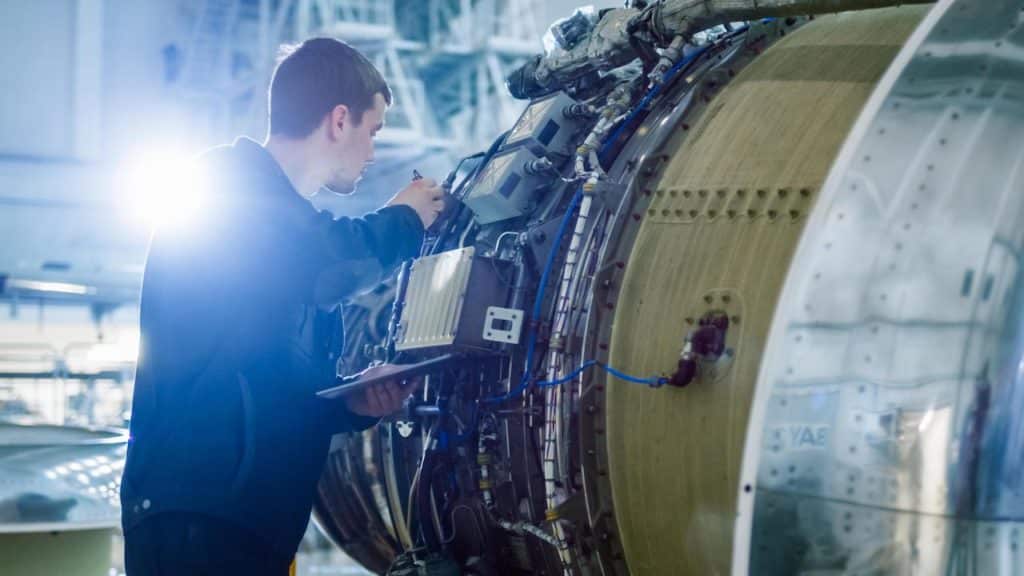
The process begins with careful planning, identifying the best route for the engine part’s journey. Here, expertise in managing Time Critical deliveries shines, ensuring parts arrive exactly when needed. We communicate in your language and can get you a quote within 30 minutes, allowing you to focus on your operations. It’s about being prepared to navigate the unexpected, a trait that comes only with over 30 years of industry experience.
High-value items like aircraft engine parts require extra care due to their delicate nature. We understand the significance of these shipments. Our well-trained and professional On-Board Couriers can hand carry your Time Critical delicate parts to the required destination. High level visibility throughout the entire journey gives you peace-of-mind. Some aircraft parts are classified as dangerous goods. These parts introduce an additional layer of complexity, as components like fuel control units, power supplies, and oxygen generators require handling with the utmost caution. They need special packaging, specific labels, and controlled transportation conditions. Navigating these safety requirements is a complex task. It requires a deep understanding of international regulations for shipping dangerous goods. Yet, with our expert assistance, it’s entirely manageable. As specialists in the field, we are equipped to handle such sensitive shipments, maintaining safety, efficiency, and punctuality.
Finally, logistics coordination is key. This stage requires alignment with multiple parties, such as customs, carriers, and consignees. Having set up 24/7/365 Global Control Towers, we enable a swift response to changes or disruptions in the supply chain.
In the world of aviation logistics, every second counts. It’s a world where timeliness is of the essence and where delays can cause significant disruptions. With the right approach and our 30 years of experience in providing customized Time Critical solutions in Aerospace & Aviation, you can rest assured that we can make it happen for you!